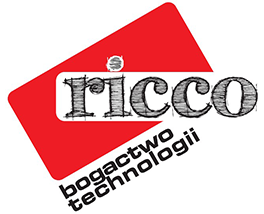
Firma Dreher jest producentem młynów do rozdrabniania odpadów z tworzyw termoplastycznych. Są to zarówno małe „młynki” o wydajnościach od kilkudziesięciu kilogramów na godzinę do dużych młynów o wydajnościach kilku ton na godzinę.
Obszary zastosowań młynów Dreher mogą mieć miejsce w branżach, w których przetwarzane są tworzywa termoplastyczne. Z jednej strony jest to recykling „brudnych” odpadów. Z drugiej jest to rozdrabnianie czystych odpadów produkcyjnych powstałych przy produkcji folii, przy produkcji butelek i pojemników, przy termoformowaniu, przy wtrysku itp.
Film przedstawiający siedzibę i fabrykę DREHER.
Młyny produkowane przez firmę Dreher przeznaczone są do rozdrabniania odpadów z tworzyw termoplastycznych.
W przypadku firmy Dreher „młyny” oznacza zarówno pojedyncze maszyny do rozdrabniania (właściwy młyn) jak również i kompletny system do rozdrabniania, w którym młyn może być uzupełniony o systemy podawania odpadów, system odbioru rozdrobnionego odpadu, obudowę dźwiękoszczelną itp.. Dreher wykonuje też projekty inżynieryjne takich kompletnych instalacji pod konkretne zapytanie klienta.
Użytkownikami młynów Dreher w Polsce zostają firmy, które:
– mają bardzo zabrudzony odpad (zalecamy wtedy wersję mokrą pracy młyna),
– mają trudny do rozdrobnienia odpad,
– chcą związać się z wiarygodnym dostawcą,
– dążą do zminimalizowania jednostkowych kosztów operacyjnych.
Film przedstawiający działanie młynów DREHER.
Włoska firma Elba została założona w 1956 roku i od 1964 roku jest producentem zgrzewarek do produkcji różnego rodzaju torebek, worków, reklamówek, T-Shirt’ów, itp. Różne rodzaje zgrzewarek umożliwiają produkcję opakowań ze zwykłej folii PE czy PP, jak i z wielo-warstwowych folii barierowych z PA/PE czy termokurczliwych.
Elba (a dokładniej firmy córka Fiborsin) jest też producentem linii do produkcji siatek.
Elba jest producentem wysokowydajnych torebkarek SA-V do produkcji torebek z różnych rodzajów folii i laminatów. Jedną z ich najważniejszych cech jest uniwersalność, co wraz z modułową budową i krótkim czasem przezbrojenia sprawia, że nie mają sobie równych w sytuacjach, gdzie jest zapotrzebowanie na różnorodną i zindywidualizowaną produkcję.
Użytkownikami torebkarek SA-V Elba w Polsce zostają firmy oczekujące:
– maszyn o wysokiej wydajności,
– maszyn uniwersalnych, na których będzie można wyprodukować szerokie spektrum torebek,
– wykonania torebek z różnych materiałów,
– błyskawicznej zmiany formatów,
– niezawodnej jakości wyprodukowanych woreczków,
– sprawdzonej pozycji producenta na rynku,
– łatwo dostępnego serwisu i szybkiej dostawy części zamiennych.
Torebkarki, prezentacja firmy Elba.
Szwedzka firma FAS Converting Machinery została założona w 1978 roku. Jest producentem rolomatów, czyli zgrzewarek worków foliowych nawiniętych na rolkę (tzw. „bags on roll”).
Zakres produkowanych rolomatów jest bardzo szeroki. Mogą one być przystosowane do pracy w linii (są wtedy oferowane bez odwijaka), czyli bezpośrednio za wieżą rozdmuchową lub też mogą pracować jako samodzielne maszyny (wtedy mają własny odwijak).
Główne zastosowania rolomatów FAS są w produkcji worków śmieciowych (z banderolą lub bez, z tasiemką lub bez, typu „sinus”, itp.) lub koszulek (tzw. T-shirt’ów), zarówno składanych (typu „C” lub podwójne „C”) jak i nie składanych, z automatycznym odbiorem i układaniem rolek lub bez automatycznego odbioru, itp.
W styczniu 2024 FAS Converting Machinery zostało przejęte przez amerykańska firmę CMD. Przejęcie to oznacza, że FAS może oferować poza produkowanymi przez siebie maszynami również maszyny produkowane przez CMD. Jednocześnie ustalono, że na terenie Polski, zespół RICCO będzie reprezentował w równym stopniu FAS jak i CMD.
FAS jest producentem rolomatów do produkcji różnych rodzajów worków foliowych. Specjalnością maszyn firmy FAS jest produkcja z wykorzystaniem folii o średnich i dużych grubościach, często pochodzących z recyklingu.
Modułowa konstrukcja maszyn pozwala na dowolne konfigurowanie linii produkcyjnej i wyposażenie maszyn w zespoły produkcji różnych worków takich jak t-shirt, wave-top czy worków z tasiemką. Pozwala również na bezproblemowe doinstalowanie potrzebnych modułów w przyszłości.
Rolmaty FAS mogą mieć zastosowanie zarówno w zastosowaniach in-line jak i off-line.
Najistotniejsze zalety maszyn FAS to:
– kompaktowe rozmiary powodują, że zgrzewarki zajmują bardzo mało miejsca, co jest ważne w przypadku użytkowników dysponujących ograniczoną powierzchnią na hali,
– unikalne rozwiązanie techniczne do produkcji worków śmieciowych typu „sinus” wiązanych krzyżowo (zamiast tasiemki).
Użytkownikami rolomatów FAS w Polsce zostają firmy, które:
– szukają prostych, ekonomicznych i skutecznych rozwiązań w zakresie produkcji worków na rolce,
– oczekują stabilnej i powtarzalnej produkcji,
– oczekują profesjonalnego wsparcia serwisowego.
Rolomaty – animacja linii T-Shirt.
Firma Hamer jest dostawcą zindywidualizowanych linii do produkcji i pakowania blistrów oraz linii termoformujących. Istotą tej działalności jest więc zrozumienie potrzeb potencjalnego użytkownika w obszarze produkcji blistrów i pojemników termoformowanych w celu zaoferowania, a następnie wykonania optymalnego rozwiązania.
Typowe etapy w produkcji blistrów to:
– formowanie blistrów,
– pakowanie produktów do blistrów,
– operacje dodatkowe np. wkładanie kartonika, wycinanie otworu, itp.,
– zamykanie blistrów i ich wycinanie,
– rozładunek i zbiorcze pakowanie blistrów.
Produkowane przez Hamer linie mogą być z pełnym automatycznym pakowaniem produktów do blistrów bądź też mogą być wyposażone w stół pakujący, przy którym operatorzy ręcznie wkładają produkty do blistrów.
Możliwość wykonania indywidulanych systemów wynika z faktu, że cały proces produkcyjny linii do blistrów i termoformowania począwszy od projektu maszyn, poprzez ich produkcję a na wytwarzaniu narzędzi kończąc odbywa się wewnątrz firmy Hamer.
Użytkownikami linii do blistrów Hamer w Polsce są klienci oczekujący:
– indywidualnie skonfigurowanej maszyny pod ich potrzeby,
– pełnej automatyzacji linii wdrożonej od razu lub stopniowo,
– solidnego producenta o szybkiej reakcji serwisowej.
Linia do blistrów – BPC23.
Linia do blistrów – HC63.
Linia do blistrów – BPC35H.
Hosokawa Solids produkuje transporty pneumatyczne i kompletne systemy obsługi materiałów sypkich. Jest wiele różnych rodzajów transportu pneumatycznego (podciśnieniowy, nadciśnieniowy, partiami, z dodatkowym doprowadzeniem powietrza i wiele innych). Dobór rodzaju dla danego transportu zależy od właściwości produktu, który ma być przesyłany.
Użytkownikami transportów pneumatycznych Hosokawa Solids zostają w Polsce firmy, które:
– mają trudne produkty do transportu (np. sadza, biel, śmietanka 60% itp.),
– zainteresowane są posiadaniem kompletnej instalacji do obsługi materiałów sypkich.
Transporty pneumatyczne – kompletny system obsługi materiałów sypkich.
Niemiecka firmy Hydrodyn (należąca do austriackiej grupy NGR) jest dostawcą technologii i maszyn dla recyklingu odpadów z tworzyw sztucznych.
Z jednej strony firma zajmuje się więc modernizacjami istniejących już linii recyklingowych (inżyniering i / lub dostawa maszyn uzupełniających) jak również projektowaniem nowych linii. W obu tych sytuacjach po wykonaniu projektu klient może zakupić dowolnie wybrane przez siebie maszyny nawet od innych producentów.
Z drugiej strony firma zajmuje się produkcją i sprzedażą własnych maszyny i kompletnych linii do recyklingu tworzyw. Unikalność maszynowa dotyczy nie tylko rozwiązań technicznych w pewnych maszynach np. opatentowana myjka HydroCleaner, ale również niespotykanej nigdzie indziej „kontenerowej” koncepcji zestawiania kompletnych linii. Gotowe moduły o wymiarach kontenerów 10-cio i 20-sto stopowych mogą być bowiem dowolnie konfigurowane w zależności od potrzeb konkretnego klienta.
Firma Hydrodyn zajmuje się inżynieringiem linii do recyklingu odpadów z tworzyw sztucznych.
– w przypadku istniejących linii recyklingowych Hydrodyn może przeprowadzić ich audyt a następnie zaproponować projekt przebudowy linii eliminujący jej wąskie gardła;
– dla nowych linii recyklingowych firma może wykonać kompletny projekt inżynieryjny linii.
W obu wypadkach wykonany projekt pozostaje własnością klienta, który może zakupić maszyny wg własnego uznania.
Użytkownikami usług projektowo – modernizacyjnych Hydrodyn zostają klienci, którzy chcą usprawnić swój istniejący proces produkcyjny eliminując z niego wąskie gardła lub maszyny nie osiągające pełnej efektywności.
Myjka do odpadów tworzywowych HydroCleaner jest unikalnym (opatentowanym) rozwiązaniem firmy Hydrodyn. Mycie (oczyszczanie) odpadów odbywa się w wodzie, w której głównym czynnikiem czyszczącym są siły tarcia pochodzące od statora i rotora. W ten sposób z masy odpadowej podawanej na wejściu do HydroCleaner’a usuwane są nie tylko zanieczyszczenia nie związane z tworzywem (piasek, papier itp.), ale również te, które są trwale z nim związane (nadruki, oleje, kleje, etykiety itp.). Proces mycia następuje bez żadnych chemikaliów, tylko dzięki samej wodzie i sile tarcia.
Użytkownikami myjki HydroCleaner lub innych urządzeń, bądź kompletnych linii Hydrodyn zostają klienci, którzy muszą uzyskać wysokiej jakości produkt końcowy, a jednocześnie mają ograniczoną powierzchnię do dyspozycji.
Kompletne linie do recyklingu Hydrodyn składają się zasadniczo z dwóch części: mycia wstępnego i uszlachetniania końcowego. Obie części są od siebie oddzielone i mają swoje własne, niezależne obiegi wody myjącej. Unikalną cechą linii Hydrodyn jest ich „kontenerowa” budowa. Każdy z elementów linii (np. mycie, separacja, suszenie) jest wbudowany w jeden lub więcej klocków o wielkości typowego kontenera 10-cio lub 20-sto stopowego. Poprawność działania modułów jest w łatwy sposób testowana w zakładzie Hydrodyn przed wysyłką. Ponieważ moduły są typu plug & play, to montaż całej linii u klienta jest błyskawiczny.
Użytkownikami myjki HydroCleaner lub innych urządzeń, bądź kompletnych linii Hydrodyn zostają klienci, którzy muszą uzyskać wysokiej jakości produkt końcowy, a jednocześnie mają ograniczoną powierzchnię do dyspozycji.
Włoska firma ICMA San Giorgio założona w 1907 roku, od 1965 jest producentem różnego typu linii opierających się na współbieżnych wytłaczarkach dwuślimakowych. W szczególności są to linie do produkcji compoundów z materiałów oryginalnych bądź pochodzących z recyklingu (zawierające systemy do podawania i obsługi surowców, jak również systemy pakowania finalnego produktu w worki lub big bagi) oraz linie do wytłaczania różnego typu profili lub arkuszy z compoundingiem realizowanym w linii.
ICMA San Giorgio produkuje kompletne linie oparte na wytłaczarkach dwu ślimakowych służące do re-cyklingu, up-cyklingu i re-compoundingu.
RE-cykling – typowa re-granulacja odpadów wymagających mocnego odgazowania i dobrego filtrowania (np. wilgotnych, zadrukowanych, odpadów wielowarstwowych itp.),
UP-cykling – mieszanie co najmniej dwóch rodzajów tworzyw, często niezgodnych ze sobą, w celu osiągnięcia produktu o wyjątkowych właściwościach (np. odpady z zużytego sprzętu elektrycznego i elektronicznego WEEE),
RE-compounding – dodawania (wmieszania) do stapianych odpadów materiałów nieplastycznych (np. wypełniaczy mineralnych, wypełniaczy naturalnych (robienie produktów eko), włókien).
Użytkownikami linii do compoundów ICMA w Polsce zostają firmy, które:
– chcą przerabiać nietypowy materiał lub materiały, gdzie wskazane byłoby przeprowadzenie testów i doświadczenie producenta maszyn z identycznym lub podobnym materiałem (materiałami),
– zamierzają w produkować innowacyjne re-granulaty przy maksymalnie niskich kosztach produkcji,
– poszukują jednego, kompleksowego dostawcy dla całej linii recyklingu (od rozładunku surowców poczynając, na zapakowanym produkcie gotowym do wysyłki kończąc).
Założona w 1961 roku firma MACCHI była jednym z pierwszych na świecie producentów linii do rozdmuchu folii.
Macchi należy obecnie do wiodących producentów linii do rozdmuchu folii. Jest to praktycznie jedyna linia produkowa Macchi, więc cała działalność firmy koncentruje się tylko i wyłącznie na liniach do rozdmuchu folii. Firma zapewnia swoim Klientom maszyny wysokiej niezawodności z korzystnym stosunkiem ceny do wydajności. Buduje według specyfikacji, a nie według kosztów.
Od samego początku firma Macchi skupiała swoje wysiłki na ulepszaniu i rozwijaniu technologii współwytłaczania, osiągając wiodącą rolę w sektorze folii dzięki zaangażowaniu w innowacje, ciągłe inwestycje w badania i rozwój, jakość, niezawodność produktów oraz nacisk na elastyczność i wszechstronność.
Technologie wytłaczania folii Macchi.
Produkowane przez Macchi linie do rozdmuchu folii pokrywają praktycznie wszystkie możliwe zapotrzebowania klientów: liczbę warstw, oczekiwane szerokości i grubości folii, wydajność, możliwe do użycia surowce, końcowe zastosowanie folii itp.
Niektóre z komponentów linii do rozdmuchu folii mogą być sprzedawane pojedynczo do zastosowań w już istniejących liniach produkcyjnych. Takimi komponentami są np.: platformy ekstruderów Coex Flex, nawijaki serii BO, regranulatory do krawędzi folii Recotrim. Takie dostawy komponentów umożliwiają użytkownikom szybką modernizację istniejących linii do aktualnych wymagań w budżecie wielokrotnie niższym niż budżet na kompletną nową linię.
Wszystkie wyprodukowane przez Macchi linie i pojedyncze komponenty wysyłane są po obowiązkowych testach produkcyjnych z materiałem, niezależnie od tego, czy klient jest czy nie jest przy nich obecny.
Użytkownikami linii Macchi w Polsce zostają firmy oczekujące:
– maszyn o wysokiej wydajności,
– maszyn uniwersalnych, na których będzie można wyprodukować szerokie spektrum folii,
– niezawodnej jakości wyprodukowanej folii,
– sprawdzonej pozycji producenta na rynku,
– łatwo dostępnego serwisu i szybkiej dostawy części zamiennych.
9-warstwowa linia do współwytłaczania.
RECOTRIM to unikalny system granulowania, opracowany w celu umożliwienia recyklingu na linii produkcyjnej ścinków bocznych powstałych podczas wytłaczania folii. Standardowo wyposażona jest w lej oddzielający powietrze od ścinków, co jest bardzo przydatne, gdy nawijarka jest wyposażona w system ssący Venturi umożliwiający usuwanie ścinków, ale na życzenie można go uzupełnić o wałek dociskowy, którego prędkość odpowiada prędkości nawijarki.
Typową cechą RECOTRIM jest zastosowanie przeciwbieżnej podwójnej śruby, umożliwiającej płynne podawanie materiałów o dowolnej grubości. Po podaniu materiał jest topiony i uplastyczniany w ślimaku, bez utraty jakichkolwiek właściwości fizycznych, a następnie podawany do specjalnie zaprojektowanej matrycy wytłaczającej, w oparciu o koncepcje przepływu stopu wywodzącej się z wytłaczania folii, i wychodzi przez dyszę pasma. Tam obrotowy system cięcia z regulowaną prędkością dzieli wytłaczane pasma na peletki o wymaganej wielkości, które następnie są chłodzone powietrzem przed wyładowaniem do pojemnika.
System wyposażony jest w zsyp boczny, który umożliwia również odzysk zwojów odpadów.
Wydajność RECOTRIM różni się w zależności od rodzaju materiałów i może osiągnąć nawet 50 kg/h przy prędkości podawania 120-130 m/min.
Użytkownikami systemu do regranulacji Macchi zostają w Polsce fimy:
– mające czysty odpad poprodukcyjny w nierozdrobnionej postaci i chcące go w prosty sposób przetworzyć na regranulat,
– poszukujące kompaktowej, energooszczędnej i niemal bezobsługowej maszyny do regranulacji.
Firma MacDue została założona w 1981 roku. Dziś MacDue jest wiodącym producentem zautomatyzowanych linii pakujących dla różnych sektorów przemysłowych.
Najważniejsze z nich to:
– pakowanie papierów higienicznych (ręczników, toaletowych, chusteczek) na rolkach lub składanych,
– pakowanie worków foliowych w rolkach np. worków na odpady,
– pakowanie płyt izolacyjnych EPS i XPS,
– pakowanie tacek i kubeczków termoformowanych,
Z ponad 7500 maszynami zainstalowanymi na całym świecie, MacDue oferuje kompletne usługi, w tym doradztwo, projektowanie, zarządzanie projektami, produkcję, instalację i obsługę posprzedażną dla swoich linii pakujących i maszyn, które idealnie pasują do procesu produkcyjnego i układu klienta.
Użytkownikami pakowaczek MACDUE w Polsce zostają firmy, które:
– cenią rozwiązania techniczne przyjazne dla użytkownika,
– oczekują elastycznych rozwiązań pozwalających na adaptację do szybko zmieniających się oczekiwań marketingu (nowe opakowania, nowe formaty itp.),
– poszukują stabilnych partnerów na lata o ugruntowanej pozycji rynkowej.
Dla produkcji worków na rolce np. worków na śmiecie MacDue oferuje kompletne linie pakujące (lub pojedyncze maszyny) począwszy od pierwszego pakowania pojedynczych rolek lub ich pakietów w folie, poprzez pakowanie zbiorcze do kartonów, aż do paletyzacji.
Użytkownikami pakowaczek MacDue w Polsce zostają firmy, które:
– cenią rozwiązania techniczne przyjazne dla użytkownika,
– oczekują elastycznych rozwiązań pozwalających na adaptację do szybko zmieniających się oczekiwań marketingu (nowe opakowania, nowe formaty itp.),
– poszukują stabilnych partnerów na lata o ugruntowanej pozycji rynkowej.
MacDue oferuje kompletne linie lub pojedyncze urządzenia do pakowania płyt izolacyjnych XPS i EPS takie jak grupowanie płyt, pakowanie w folie, etykietowanie, paletyzowanie.
Użytkownikami pakowaczek MacDue w Polsce zostają firmy, które:
– cenią rozwiązania techniczne przyjazne dla użytkownika,
– oczekują elastycznych rozwiązań pozwalających na adaptację do szybko zmieniających się oczekiwań marketingu (nowe opakowania, nowe formaty itp.),
– poszukują stabilnych partnerów na lata o ugruntowanej pozycji rynkowej.
Dla produkcji kubeczków i tacek termoformowanych MacDue oferuje kompletne linie pakujące (lub pojedyncze maszyny) począwszy od pierwszego pakowania stosów w folie, poprzez pakowanie zbiorcze do kartonów, aż do paletyzacji.
Użytkownikami pakowaczek MacDue w Polsce zostają firmy, które:
– cenią rozwiązania techniczne przyjazne dla użytkownika,
– oczekują elastycznych rozwiązań pozwalających na adaptację do szybko zmieniających się oczekiwań marketingu (nowe opakowania, nowe formaty itp.),
– poszukują stabilnych partnerów na lata o ugruntowanej pozycji rynkowej.
Austriacka firma NGR została założona w 1996 roku. Jest producentem pojedynczych maszyn bądź kompletnych linii do regranulacji opadów z tworzyw sztucznych.
Historycznie najważniejszym produktem NGR jest sytem S:GRAN, w którym występuje unikalne (bo opatentowane) rozwiązanie połączenie szredera i wytłaczarki w prostopadłym ustawieniu ich osi i o niezależnych napędach.
W ostatnich latach firma NGR rozpoczęła produkcję reaktorów do płynnej polikondensacji PET. Reaktory te mogą być wstawiane do istniejących lub nowych linii wytłaczających produkty z PET pozwalając zastępować materiał oryginalny i dając jednocześnie gwarancję wysokiej jakości produktu końcowego.
Linie do regranulacji NGR mogą występować w różnych konfiguracjach takich jak:
– wytłaczarka ze szrederem przeznaczona do odpadów czystych nie wymagających mycia (unikalnym rozwiązaniem jest prostopadłe ułożenie osi szredera i ekstrudera, z których każde ma swój oddzielny napęd, ze względu na patent NGR takie rozwiazanie jest dostępne tylko w maszynach NGR),
– wytłaczarka z zagęszczarką przeznaczona do umytych płatków.
Dzięki unikalnej konfiguracji wytłaczarka ze szrederem umożliwia bezproblemowe przerabianie różnych form odpadu takich jak np. zlepy, rolki folii czy włókna a nawet rury.
Najistotniejsze zalety konfiguracji wytłaczarki ze szrederem to:
– zastąpienie klasycznych wielo-stopniowych systemów do regranulacji przez jedną kompaktową maszyną,
– możliwość przerabiania bardzo różnych postaci materiału bez konieczności wstępnego rozdrobnienia,
– krótka droga i czas przebycia materiału w maszynie, a tym samym mniejsza jego degradacja (lepsza jakość regranulatu).
Użytkownikami linii do re-granulacji NGR zostają firmy:
– mające czysty odpad poprodukcyjny w nierozdrobnionej postaci i chcące go w prosty sposób przetworzyć na re-granulat,
– poszukujące kompaktowej, energooszczędnej i niemal bezobsługowej maszyny do re-granulacji.
S-GRAN wydajność 150-700 kg/h.
X-GRAN wydajność 1-2 t/h.
Linie do płynnej polikondensacji (Liquid State Polycondesation) odpadów PET są unikalną technologią dostarczaną przez NGR. Centralną jednostka linii LSP jest reaktor, w którym zachodzi proces płynnej polikondensacji. Może on być umiejscowiony w różnych konfiguracjach. Np. w istniejącej linii do produkcji wyrobów PET może być umiejscowiony pomiędzy ekstruderem a urządzeniami down stream. W nowych liniach, w zależności od wielkości produkcji, możemy go dostarczać z jedno lub dwuślimakową wytłaczarką, w linii do produkcji granulatu, folii, arkusza, tekstyliów itp.
Kluczowe cechy LSP:
– proces LSP jest ciągły, więc zmiana materiału może nastąpić niemal natychmiast
– wartość IV jest sterowana w linii, więc otrzymamy takie IV na wyjściu, jakie ustawimy
– odfiltrowanie ewentualnych zanieczyszczeń z fazy płynnej jest niemal idealne, więc jakość końcowa materiału jest bardzo wysoka
– czas trwania LSP jest około 60 razy krótszy niż tradycyjnego procesu SSP
– główną czynnością związaną z eksploatacją LSP jest przeczyszczenie raz na tydzień systemu próżniowego, wykonuje się to w trakcie pracy, więc nie ma potrzeby zatrzymywania procesu
– cała instalacja LSP jest dużo niższa i zajmuje dużo mniej miejsca w porównaniu z SSP.
Wszystkie cechy LSP firmy NGR powodują, że takie linie z reguły zwracają się w ciągu mniej niż jednego roku.
Użytkownikami lini do płynnej polikondensacji odpadów PET firmy NGR zostają w Polsce firmy, które:
– w produkcji swoich wyrobów z PET zwiększają udział surowców pochodzących z recyklingu,
– w procesie zastępowania surowców oryginalnych przez odpadowe nie mogą dopuścić do obniżenia jakości produkowanych przez siebie wyrobów,
– chcą zachować pełną kontrolę nad parametrami surowca PET i dostosować je każdorazowo do aktualnych wymogów produkcyjnych,
– przywiązują wagę to tego, żeby instalacja zajmowała jak najmniej miejsca i była jak najbardziej energooszczędna.
Linia do płynnej polikondensacji odpadów PET.
Włoska firma OMSO została założona w 1952 roku. Jest producentem drukarek fleksograficznych i sitodrukowych. Nadruki można wykonywać na pojemnikach (kubkach) termoformowanych, na pojemnikach wydmuchiwanych (butelki, kanistry) i na tubkach wytłaczanych.
OMSO jest prekursorem i do dziś dnia pozostaje liderem technologii zastosowania serwomotorów w drukarkach z wymienionego wyżej obszaru zastosowań. Pierwszą drukarką tego typu była drukarka SERVOTUBE przeznaczona do druku fleksograficznego na tubkach kosmetycznych. Identyczną drukarką wprowadzoną do produkcji w drugim kroku była SERVOCUP przeznaczona do druku na kubkach termoformowanych. Następna serią maszyn była SERVOBOTTLE przeznaczona do sitodruku na butelkach. Osiągnięcie jakości druku fleksograficznego w tych nowych obszarach stanowiło przełom w technologii zdobienia.
OMSO produkuje drukarki do tubek i butelek. Konstrukcja drukarki pozwala na dowolną konfigurację stacji do nadruku flexo lub sitodruku.
Użytkownikami drukarek do tubek i butelek OMSO zostają w Polsce firmy, które oczekują:
– wysokowydajnego druku na tubkach i butelkach,
– wysokiej jakości techniki flexo i sitodruku.
Drukarki do tubek i butelek.
PLASTIBLOW (znana również pod nazwą Plastimac) jest wiodącym światowym dostawcą maszyn do wytłaczania z rozdmuchem dla przemysłu przetwórstwa tworzyw sztucznych. Duża liczba zadowolonych klientów używa maszyn PLASTIBLOW do produkcji plastikowych butelek, pojemników i pustych przedmiotów dla szerokiego zakresu branż, takich jak kosmetyczna, higieny osobistej, farmaceutyczna, medyczna, spożywcza, chemiczna i motoryzacyjna.
PLASTIBLOW (znana również pod nazwą Plastimac) od 1964 roku produkuje linie do ciągłego wytłaczania z rozdmuchem różnego typu butelek, kanistrów i elementów technicznych. W tej chwili są to już tylko maszyny elektryczne do produkcji pojemników jedno lub wielo-warstwowych.
Użytkownikami maszyn Plastiblow w Polsce zostają firmy oczekujące:
– maszyn o wysokiej wydajności,
– maszyn uniwersalnych, na których będzie można wyprodukować szerokie spektrum opakowań,
– wykonania opakowań z różnych materiałów,
– błyskawicznej zmiany formatów,
– niezawodnej jakości wyprodukowanych opakowań,
– sprawdzonej pozycji producenta na rynku,
– łatwo dostępnego serwisu i szybkiej dostawy części zamiennych.
Przegląd produkcji Plastiblow, film korporacyjny.
Pojemniki dla produktów do czyszczenia, dezynfekcji, odkażania.
PB22ED 700 Coex3 ekstruzja z rozdmuchem.
EBM machine mod PB26ED – 900 DECO.
Vollenda produkuje pakowaczki worków pakujące materiały sypkie do worków (foliowych, papierowych, wentylowych itp.) 5-50 kg. Mogą to być pakowaczki w pełni automatyczne, bądź tylko półautomatyczne. Mogą to być same pakowaczki lub też z urządzeniami towarzyszącymi np. z kompletną linią do paletyzacji worków.
Użytkownikami pakowaczek worków Vollenda zostają w Polsce firmy, które:
– oczekują szybkich i dokładnie ważącyh maszyn,
– dbających o produkcyjne środowisko pracy (brak pylenia),
– muszą spełniać w swojej produkcji różne normy np. ATEX.
RICCO INTERNATIONALTRADE & CONSULTANCY
ul. Reymonta 34
05-082 Latchorzew
tel.: 22 867 8450
ricco@ricco.com.pl
RICCO INTERNATIONALTRADE & CONSULTANCY
ul. Reymonta 34
05-082 Latchorzew
tel.: 22 867 8450
ricco@ricco.com.pl